
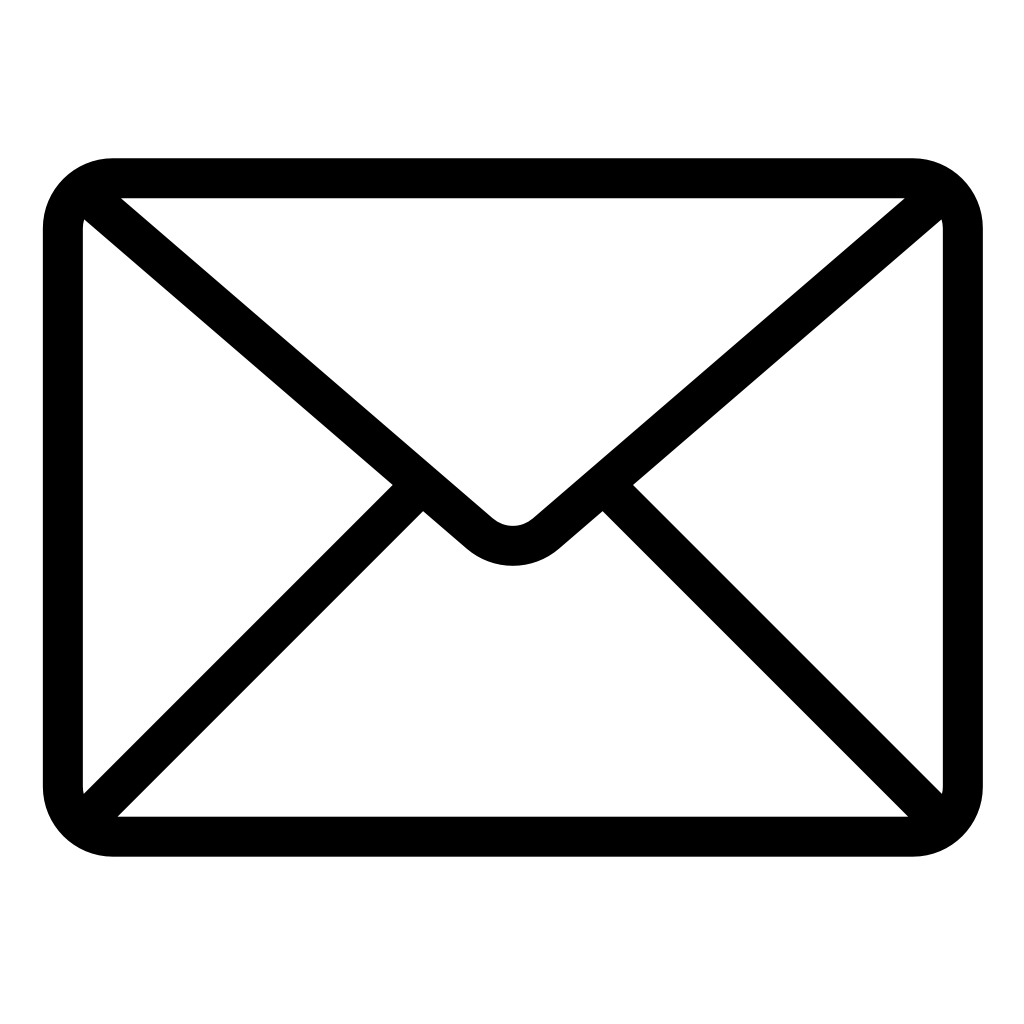
Key technical points of development of fan bearing
keywords: spindle bearing, Wind power bearing, technical requirements, design, development
Bearings for wind turbines can be roughly divided into three categories, namely: yaw bearings, paddle bearings, transmission system bearings (spindle and gearbox bearings). It is difficult to design and manufacture because of its complex use environment and high requirement of reliability and life. Based on the domestic and foreign practical experience and research results, this paper briefly explains the design characteristics and technical requirements of fan bearings, as well as matters needing attention in development and selection.
The supporting bearings of wind generator are mainly used in yaw system, slurry system, transmission and engine, etc. Each unit mainly includes 1 set of yaw bearing, 2 sets of wind blade spindle bearing, 15 sets of gearbox bearing, 2 sets of generator bearing, and many types of bearing structure.
1. code method
There is no exact information about the code of foreign manufacturers' wind turbine bearings. The code method of yaw and variable blade bearings of domestic wind turbines adopts the code method of rotary plate bearings in JB/T 10471-2004. However, there are double row four-point contact ball rotary plate bearings in the yaw and variable blade bearings of wind turbines. The code of this structure bearing is not specified in JB/T 10471 -- 2004. Therefore, the code of double-row four-point contact ball rotary bearing is added to the wind power bearing standard. Because the structure type of single row four point contact ball rotary bearing is expressed by 01 code, and 02 code indicates the structure type of double rejection reducing diameter ball rotary bearing, so the company uses 03 code to indicate the structure of double row four point contact ball rotary bearing.
2. Technical requirements
2.1 Basic Requirements
Wind turbines work in the field all the year round, the working conditions are harsh, the temperature, humidity and bearing load vary greatly, the wind speed can reach up to 23m/s, and with impact load, so the bearing is required to have good sealing and lubrication performance, impact resistance, long life and high reliability. Because the generator needs to start when the wind is 2-3, and can rotate with the change of wind direction, it needs special bearing structure design to ensure that it meets the requirements of low friction and high sensitivity. In the design and manufacture, the material processing, heat treatment, lubrication, sealing and corrosion protection of large yaw bearings with outer ring teeth have particularly high requirements, which need to be specially designed and studied. The life of the main engine of the wind turbine is set to 20 years. Therefore, the reliability life of the wind turbine bearing is required to be the same as the life of the unit, and more than 20 years, because the bearing installation position is not easy to disassemble and assemble, and the disassembly cost is high, and the cycle is long.
2.2 Installation Parts
In the fan rotor spindle, gear box (speed up machine), generator, yaw gear box (reducer), and yaw rotating seat, blade pitch moment rotating seat, hydraulic pump and other parts are used bearings. Yaw bearings are installed at the connection part between the tower and the cockpit, and paddle bearings are installed at the connection part between the root of each blade and the hub. Among them, the paddle and yaw bearings used for the paddle and yaw system are oversized rotary plate bearings.
2.3 Design Requirements
2.3.1 Rotor spindle bearing
The rotor spindle bearing should be started, accelerated, decelerated and stopped repeatedly and irregularly when subjected to varying loads. Therefore, in addition to the study of rotor spindle bearing design, the bearing type, bearing clearance, bearing roller number, convex surface processing, cage structure and other conditions, especially for the use of bearing parts of the minimum load, average load, maximum load, and the best technical conditions are particularly important.
The design should take into account the necessary strength of the axle box and the deformation of the axle box under the maximum load and the average load. It is necessary to study the bearing life, select the thin axle box design without additional redundancy, and fully calculate the life of the spindle bearing in practice.
In addition, it is necessary to consider the deformation of the axle box and the outer ring raceway surface, calculate the load of each rolling body, and calculate the life of the rotating ring and the fixed ring.
In accordance with ISO,IEC,GL and other international regulations for the calculation of bearing theoretical life guidelines. The calculation basis is: the working time is 175,000 hours (20 years) or more, the safety rate (static rated load/static equivalent load) 2.0.
The theoretical life of bearings is calculated by the following formula:
Lmnh=aISO×106/60n (C/P) P
AISO: Life correction factor
N: Rotation speed (min-1)
C: Basic dynamic rated load (N)
P: dynamic equivalent load
P: ball bearing P =3; Roller bearing P =10/3
2.3.2 Bearing for generator
Deep groove ball bearings are usually provided in the generator to support the rotor and are greased. Bearings used for generators must be protected from corrosion damage. For this reason, the outer diameter of the bearing outer ring to the side should be sprayed with a special ceramic layer. The resistance value of the bearing coated with insulating ceramic should be greater than 100M ω, and it has the insulation performance of resisting insulation damage voltage above 2KV.
2.3.3 Acceleration machine bearing
The variable propeller bearings used in the accelerating machine require high reliability, light weight and miniaturization. In particular, the bearing life of high-speed shaft is greatly affected by the combined load of axial load and radial load. Compared with the bearing of low speed shaft, this part must use both high load capacity and high speed bearing.
2.3.4 Bearing of yaw drive device
The bearing of yaw drive device should meet the characteristics of both miniaturization and large torque transmission required by the reducer, and the design section should be low and have high rigidity to withstand the torque load from the pinion. Therefore, the angular contact ball bearing used for the reducer spindle is designed to deepen the inner and outer ring raceway and improve the axial load capacity.
2.3.5 Structure
Because the rotor bearings used in wind power are not only affected by large overturning moments, but also by aerodynamic force and blade rotation and other complex fatigue loads. In addition to the requirements of high reliability and long life, more attention should be paid to the dynamic load capacity of the bearing, especially the fatigue life of the raceway, when designing the structure. Although domestic standard of variable propeller and the structure of wheel bearings make a regulation, but does not give reasonable selection of structure, from the current installed use, is analyzed.studying bearing with double row four-point contact ball bearing, yaw bearings with single row four-point contact ball bearing, also USES a small amount of cross roller or other forms.
2.4 material
The yaw and paddle bearing rings of wind power bearings are generally made of 42CrMo steel. The heat treatment adopts overall quenching and tempering treatment, and the hardness after quenching is 229HB-269Hb. The raceway part adopts surface quenching, and the quenching hardness is 55HRC-62HRC. Transmission system bearing rings are generally made of ZGGr15 or ZGGr15SiMn steel. Because the force of the yaw and variable propeller bearings of the wind generator is complex, and the impact and vibration of the bearings are relatively large, therefore, the bearing is required to withstand both the impact and the larger load. The matrix hardness of the bearing ring is 229HB-269HB, so as to ensure the bearing bearing bearing impact without plastic deformation. At the same time, the surface quenching hardness of the raceway part should reach 55HRC-62HRC, so as to increase the contact fatigue life, so as to ensure the use of long life of the bearing. In view of xinjiang, Inner Mongolia and other places where fans were installed in China in the first place, the climate temperature difference was large, the cold period was long, and the wind and sand were much, so the two major domestic companies that developed fan bearings earlier all chose the steel of South Korea Busan and Pingshan Iron and Steel Company at the beginning, whose main characteristic is that the low temperature impact energy resistance is excellent. Later, due to the long delivery cycle and rising prices, there are now switching to Japan's Sanyo company steel.
2.5 Low temperature impact energy
Wind power bearing standards require low temperature impact energy of yaw and rotor bearing ring: -20 ℃Akv, no less than 27J, and the VALUE of Akv in cold state can be determined through negotiation with users. Sometimes the working site of the wind generator may be in a very cold region, the ambient temperature is low to about -40 ℃, usually the working temperature is about -20 ℃, which requires the bearing to be able to withstand a large impact load at low temperature. Therefore, after the tempering and tempering of the bearing ring material, the low temperature impact energy test must be carried out. That is, a part of the bearing ring is taken as a sample, or a sample with the same performance and the same heat treatment condition as the bearing ring is selected for impact energy test at -20 ℃.
2.6 Supporting gear ring processing and heat treatment
Because the transmission precision of wind turbine bearing is not high, and the gear ring diameter is relatively large, the gear module is also large, therefore, the general requirements of gear according to GB/T10095.2 --2001 grade 9, or 10 precision grade processing. However, due to the impact load between the pinion and the bearing ring in the working state, the tooth surface of the bearing ring should be hardened. The tooth surface hardness of pinion gear is generally 60HRC. Considering the design requirements of equivalent life, it is stipulated that the tooth surface hardness of large gear is not less than 45HRC. Because 98% of the damage comes from the raceway in the actual use, there are special requirements for the surface quenching hardness and hardened layer of raceway, generally 55~62 HRC.
2.7 clearance
There are special requirements for yaw and variable propeller bearings in the installation of clearance. Compared with the yaw bearing, the impact load of the variable blade bearing is larger. Considering that the vibration on the blade will be large when the wind blows, the clearance of the variable blade bearing is required to be zero clearance or a slightly smaller negative clearance value, so that the fretting wear of the bearing can be reduced under the condition of vibration. Small clearance value of yaw bearing is required: 0-0.05. In addition, because the drive motor of the wind generator is driven by yaw and variable propeller bearings, it should be able to ensure that the bearing rotates the drive motor in the state of negative clearance or small clearance. Therefore, after bearing assembly, it is necessary to measure the starting friction torque without load. According to the different driving system of the main engine, the specific torque value is not the same.
2.8 lubrication
Due to the harsh field working environment and complex load of wind power bearings, they often need to work in the environment of extremely high temperature, extremely low temperature, large temperature difference between day and night and many changes in speed. It is recommended to choose the grease with strong adaptability of lithium compound grease and polyurea base grease. According to the distribution of wind turbines in China, the lubricants of wind turbine bearings are required to have low temperature resistance, extreme pressure anti-wear and thermal stability. It is generally recommended to use low temperature grease with 1# consistency containing solid additives in foreign countries, which can still lubricate below -40℃. Domestic lubricating grease can use 7011 low temperature extreme pressure grease.
According to the recommendation of Vestas, GE, Suzlon and other foreign companies, the wind power bearing previously developed by a company adopts the specified Mobil Mobil SHC 460WT grease or Shell Sheel Rhodina BBZ (variable paddle bearing) grease. And (German) Fuchs Gleitmo 585K (yaw bearing). In particular, Mobil SHC 460WT grease has excellent performance and is suitable for yaw, paddle and spindle bearings with operating temperatures ranging from -40℃ to 150℃.
2.9 the seal
The sealing material of wind power bearing is generally made of butadiene rubber (SN7453), and the structural form is lip sealing ring. In cold climate, large temperature difference in the region, the selection of fluorine rubber material sealing ring, its strong cold resistance, wide working temperature range, high temperature can be adapted to about 200℃. The double lip seal structure selected by some foreign large enterprises can effectively prevent radiation and oxidized gas from entering the bearing; In addition, for the wind field of special environment, special sealing ring material and structure design should also be considered.
2.10 Anti-corrosion treatment
As part of the installation parts of wind turbine equipment are exposed to the outside, especially the offshore wind turbine, which has been working in the corrosive salt fog environment for a long time, the sealing quality must be strictly guaranteed. It is required that the tooth surface and raceway of yaw and paddle bearings, as well as other surface parts, be treated with anti-corrosion, usually by sandblasting first, and then by thermal spraying (zinc or chromium). According to the need, the galvanized layer can be taken outside the paint protection measures.
3. conclusion
In the development of fan bearing, the main technical difficulties are the sealing structure and grease, special raceway processing method and heat treatment technology, special cage structure design and processing and manufacturing method, etc. At present, there is still a big gap between the domestic technical level and the foreign advanced level, but in recent years, some units in China have made some breakthroughs in these aspects, these research results will accelerate the process of the localization of fan bearings. The key technical points summarized by the author only serve as a launching point to inspire the thinking of those engaged in the design and development of wind power bearings, and attract attention, in order to help the research and development of domestic wind power bearings and independent innovation.